The water bottle filling machine is a highly efficient three-in-one rinsing, filling, and capping solution designed for various bottle types. It features a hanging manipulator that clamps the bottleneck, allowing easy adaptation to different bottle sizes.
This machine is ideal for filling non-carbonated beverages such as mineral water, pure water, fruit juice, milk, ice tea, alcohol, hand sanitizer, and liquid detergents. Its compact design not only saves space compared to traditional inline liquid bottling lines but also performs the bottle washing, filling, and capping processes with precision and speed.

What are the features of mineral water bottling machines?
- Compact structure. The machine features a compact design that maximizes space efficiency and integrates multiple functions into one system.
- Reasonable design. Engineered for high automation and efficiency, it ensures smooth operation and high production rates.
- High automation. Automated processes streamline operations and increase overall productivity.
- Liquid surface positioning. The filling part uses a liquid surface positioning system for precise volume control.
- Bottle compatibility. Suitable for bottles with a diameter of 50-100mm and a height of 150-320mm.
- Gravity filling. Utilizes gravity filling technology for accurate and consistent volume measurement.
- Material compatibility. Compatible with PVC and PET bottles.
- Automatic capping. The capping head is equipped with a magnetic force adjustment feature, which prevents damage by automatically slipping when the torque exceeds the set limit.
- Safety device. Includes a buzzer alarm system that ensures no bottle, no filling, and no capping, enhancing operational safety.
- Stainless steel turntable. The turntable is made of stainless steel for durability and ease of cleaning.
- Efficient bottle washing. The bottle washing system employs high-efficiency spray nozzles that clean thoroughly by spraying water at a set angle, saving water and ensuring comprehensive rinsing.
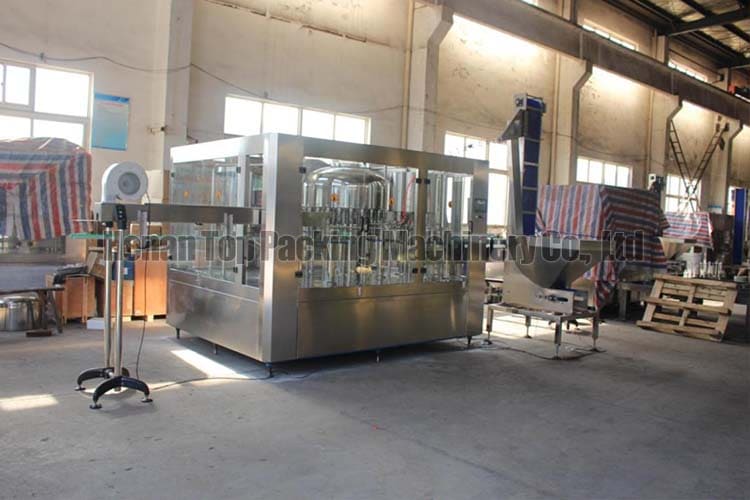
How does the 3 in 1 water bottle filling machine work?
The production process of rinsing filling capping machine
1. Bottle rinsing process
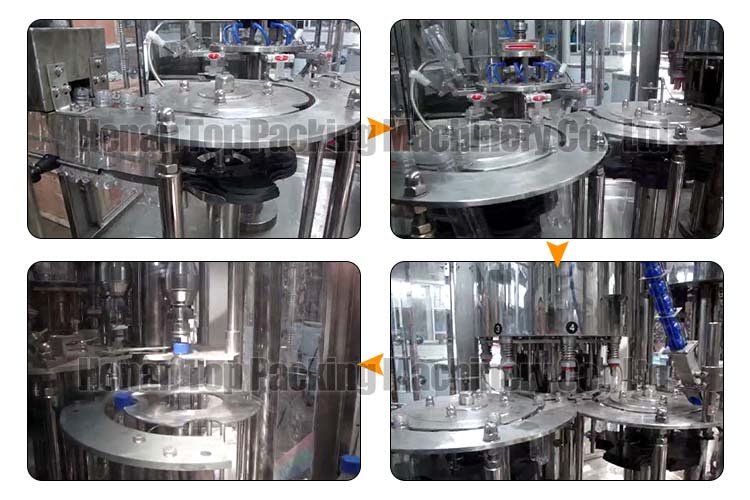
- Conveying system entry. Bottles enter the machine via the conveying system.
- Rotary disc and bottle clamp. The rotary disc in the bottle rinser clamps the bottle mouth.
- 180° rotation. The disc rotates 180° along a guide rail, positioning the bottle mouth downward into the rinser.
- Specialized rinsing. Water is sprayed from special nozzles to clean the inside of the bottle.
- Draining and rotation. After rinsing, the bottle rotates 180° to position the mouth upward.
- Transport to filling. Cleaned bottles are transported to the filling machine via the bottle conveying turntable.
2. Bottle filling and capping process
- Bottleneck support. Bottles are held by the bottleneck support part.
- Elevator mechanism. The bottles are lowered and raised by the elevator mechanism.
- Gravity filling. Gravity filling is used, with the bottle mouth rising to open the filling valve.
- Filling process. The filling valve dispenses the liquid into the bottle.
- Post-filling. After filling, the bottle mouth moves away from the filling valve.
- Neck transition dial. The bottle moves to the capping machine via the neck transition dial.
- Cap placement. As the bottle reaches the cap in the cap falling machine, the cap is placed on the bottle mouth.
- Capping. The capping machine screws the cap tightly onto the bottle.
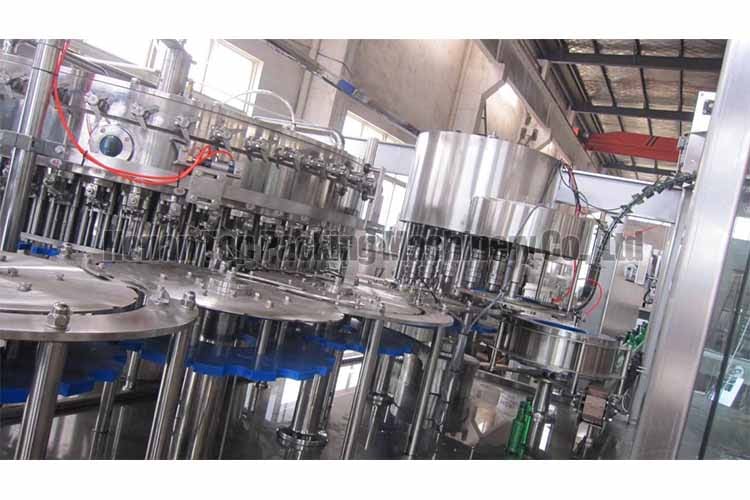
The importance of the capper in the water bottle filling machine
The bottle capping machine is an integral component of the three-in-one rinsing, filling, and capping system, renowned for its high precision. The effectiveness of the sealing process is crucial, as it directly impacts the quality of the final products.
The machine features an automatic capping mechanism designed to ensure every bottle is properly capped. If no bottle cap is present on the guide rail, the machine will automatically halt operations. This prevents the occurrence of uncapped bottles.
- Automatic capper. The machine is an automatic capper, ensuring high precision in the capping process.
- Sealing effect. The quality of the final product is directly influenced by the sealing effect of the capping machine.
- No cap, no operation. If a bottle cap is not available on the guide rail, the machine will automatically stop.
- Error prevention. This design effectively prevents uncapped bottles from being produced.
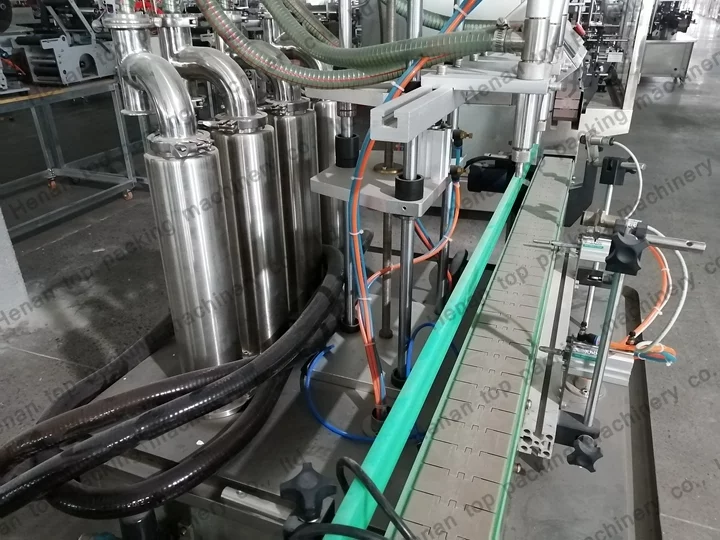
What liquid is suitable for this volumetric bottle filling machine?
The water bottle filling machine is highly versatile and is ideal for a wide range of non-carbonated beverages. It efficiently handles various liquids, including mineral water, pure water, fruit juice, milk, beverages, ice tea, skincare water, vinegar, alcohol, hand sanitizer, liquid detergent, and disinfectant water.
Moreover, the machine can be customized to accommodate different bottle categories, shapes, and sizes, providing flexible solutions to meet diverse packaging needs.
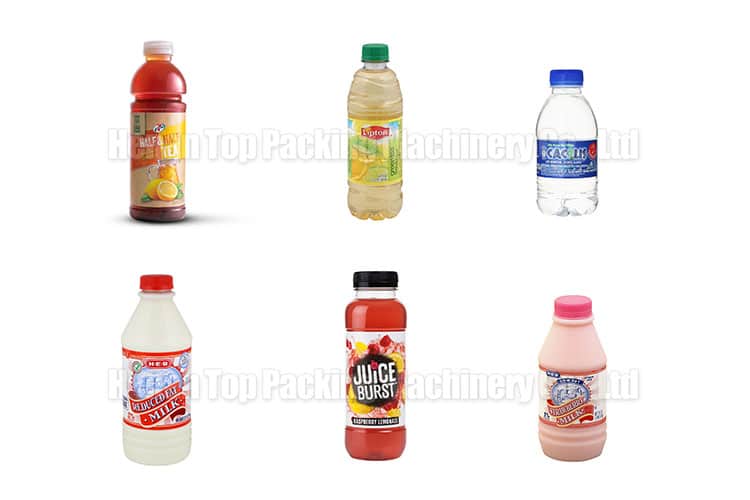
Drinking water filling machine parameter
Model | CF40-12 |
Power | 8.5KW |
Bottle diameter | 50-100mm |
Bottle height | 150-320mm |
Production speed | 1.5L/bottle, 10000Bottles/h |
The number of filling valve | 40 |
Dimension | 2800*2200*2200mm |
Weight | 5500kg |
The technical data is for your reference. For different filling volumes and the number of filling heads, the machine’s power, dimension, the weight will change according to the real situation. We offer OEM service based on our customer’s specific requirements. If you are interested in the equipment, welcome to consult us.
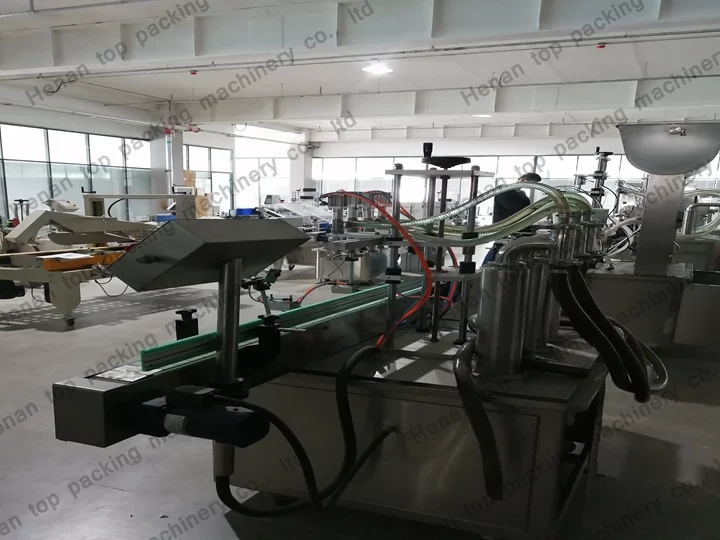
Contact us!
In conclusion, the water bottle filling machine offers a reliable and efficient solution for bottling a wide variety of non-carbonated beverages. Its advanced features, customizable options, and high precision make it a perfect choice for businesses looking to enhance their production line.
Additionally, our company provides a wide range of other packaging machines, catering to different industries and requirements. Feel free to contact us for more details or to inquire about pricing. We look forward to helping you find the ideal packaging solution!
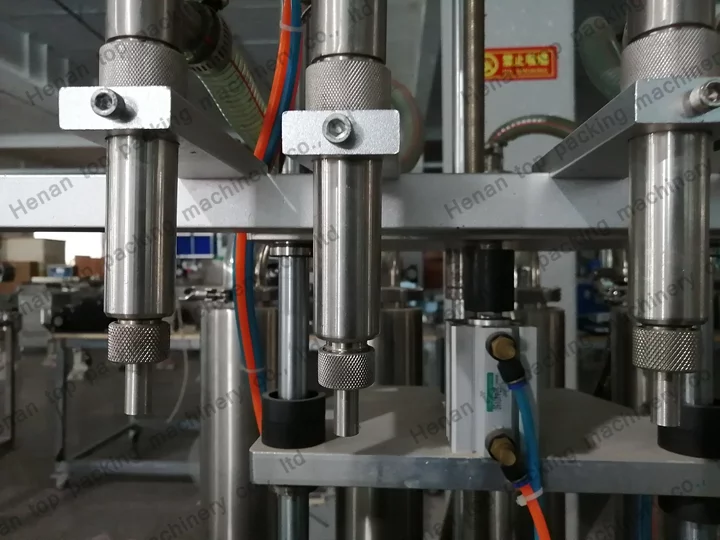