Recently, our yogurt cup filling machine was sent to Australia. Our customer, a well-established dairy products manufacturer in Australia, produces a wide range of yogurt products for local supermarkets and specialty stores.
The company has been experiencing rapid growth in demand and was looking to upgrade its production line to enhance efficiency, ensure quality consistency, and reduce manual labor costs.
Why the customer needed the machine
- Market expansion. The company required higher production capacity to meet increasing orders from retail chains and support their market expansion.
- Hygiene standards. As a food industry leader, the customer prioritized equipment that met stringent hygiene requirements and was easy to clean.
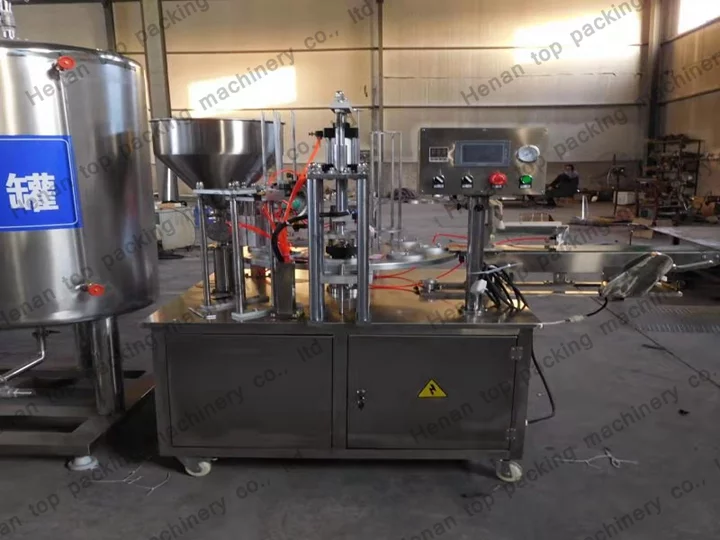
To address these challenges, the customer decided to invest in a fully automated yogurt cup filling machine.
Communication details during the transaction
- Initial inquiry:
The customer reached out to us through our website, expressing interest in a reliable yogurt cup filling machine that could handle both liquid and paste products with minimal downtime. - Understanding needs:
In our initial discussions, we identified the key requirements:- Capacity and automation. A machine capable of efficiently handling high production volumes.
- Hygiene and maintenance. A stainless-steel structure for durability, hygiene, and easy cleaning.
- Custom features. Compatibility with various cup sizes and an advanced filling system to ensure precise material quantities.
- Machine introduction:
We recommended our automatic rotary yogurt cup filling and sealing machine, highlighting the following features:- Stainless steel body. Designed to meet strict hygiene requirements and ensure durability.
- Advanced technology. Equipped with a well-known brand control system and pneumatic components for stable operation and a long service life.
- High automation. Capable of completing cup falling, material filling, cup cover placing, sealing, and product output automatically.
- Precise filling. The piston quantitative filling system allows adjustable filling volumes to ensure consistency.
- Safety sensors. Equipped with sensors that prevent filling if no cup is detected under the nozzle, reducing waste.
- Compact structure. A space-saving design with simple operation and low failure rates.
- Heat sealing. Ensures a beautiful and firm seal, minimizing leakage risks.
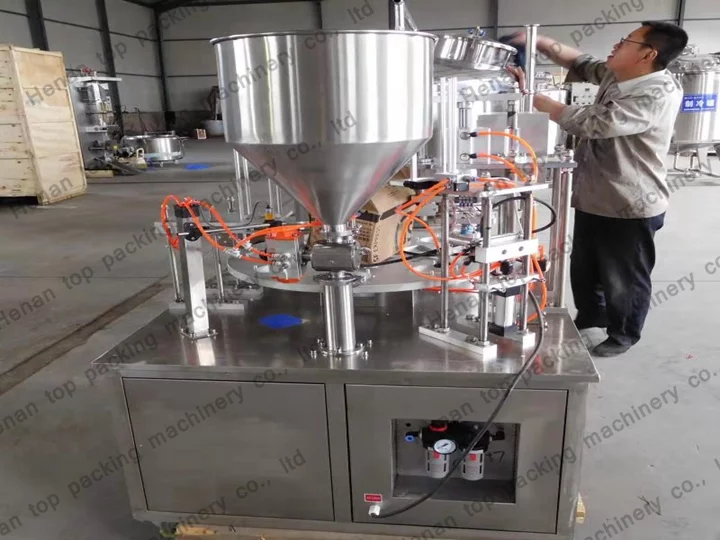
- Customization and negotiation:
The customer requested additional features, such as compatibility with specific cup sizes and integration with their existing production line. We provided technical diagrams and a tailored solution that included these customizations.- Pricing and terms. After detailed discussions, we agreed on a competitive price, including shipping and installation support.
- Delivery timeline. A delivery schedule of four weeks was finalized to ensure minimal production downtime for the customer.
- After-sales support:
We reassured the customer with our comprehensive after-sales service, including remote technical guidance and the availability of on-site support.
Outcome
The yogurt cup filling machine was delivered and installed on schedule. The customer was impressed by its performance, particularly its automation capabilities and precise filling system. They noted significant improvements in production efficiency, hygiene, and product consistency.
The client also appreciated the machine’s ability to meet hygiene standards and its ease of cleaning, which aligned perfectly with their operational requirements.
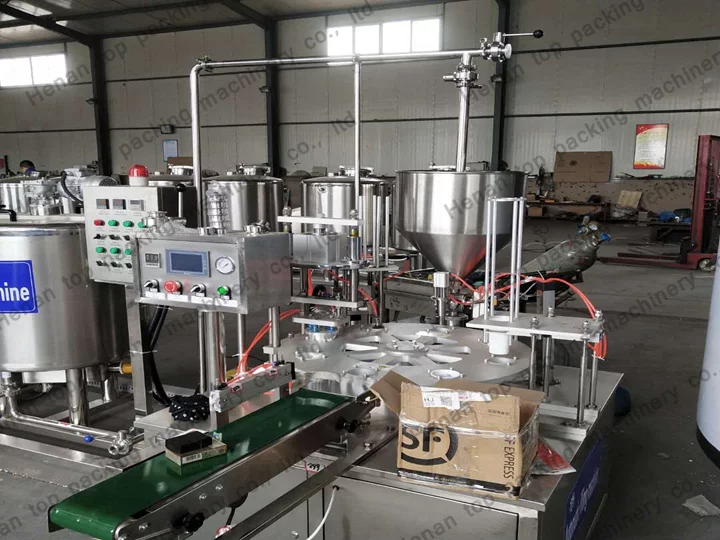
Additional offerings
In addition to yogurt cup filling machines, we also supply other packing machines. We invite you to explore our wide range of solutions and contact us for inquiries and customized solutions tailored to your needs.